Welcome To Our Blog!
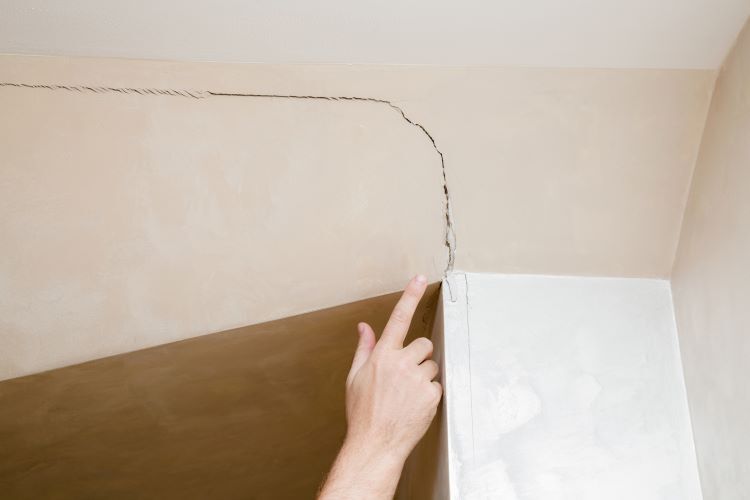
When it comes to drywall installation , achieving a flawless finish is the ultimate goal. However, even a perfect installation can lead to frustration if cracks and dents appear over time. As a homeowner or contractor in Calgary, you want durable and long-lasting walls. Here’s how to ensure your drywall stays smooth and crack-free for years to come. 1. Start with Proper Installation Techniques The foundation of crack-resistant drywall lies in meticulous installation: Secure Fastening: Use screws rather than nails to attach drywall to studs, as screws are less likely to loosen over time. Ensure they are properly countersunk but not overly tight, which can weaken the drywall. Adequate Spacing: Maintain a 1/8-inch gap between sheets to allow for natural expansion and contraction. Use a drywall spacer for consistency. Proper Stud Alignment: Ensure studs are straight and evenly spaced at 16 or 24 inches apart to prevent uneven pressure on the drywall sheets. 2. Choose the Right Materials The type of drywall and joint compound you use significantly impacts its durability: Moisture-Resistant Drywall: In Calgary's variable climate, moisture can lead to cracks. Use moisture-resistant drywall in areas like basements or bathrooms to reduce expansion-related damage. Flexible Joint Compound: Opt for a high-quality, flexible joint compound to better withstand shifts in your home’s structure. 3. Perfect the Taping and Mudding Process A professional finish relies on seamless taping and mudding: Embed Tape Properly: Use paper tape for stronger seams and ensure it is fully embedded in the joint compound to prevent peeling or cracking. Layer Gradually: Apply three thin coats of joint compound, allowing each coat to dry fully before sanding and adding the next layer. This creates a smooth, crack-free surface. Feather Edges: Feathering the edges of each layer minimizes bumps and reduces the likelihood of dents during sanding. 4. Minimize Structural Movement Homes naturally shift over time, but there are ways to mitigate its impact: Control Moisture Levels: Install dehumidifiers in high-humidity areas to prevent drywall from absorbing moisture and expanding. Ensure Strong Foundations: Cracks often appear due to foundation issues. Regularly inspect and maintain your home’s foundation to prevent structural shifting. 5. Protect During and After Installation Dents and damage often occur during construction or daily use: Avoid Impact: Use corner bead protectors and baseboard trims to shield vulnerable areas from furniture and foot traffic. Primer and Paint: Apply a high-quality primer before painting to seal the drywall surface and add an extra layer of protection. 6. Hire Professionals for Lasting Results DIY drywall installation can lead to common mistakes that compromise its durability. Hiring experienced professionals like Calgary Drywallers ensures your walls are installed and finished with expert precision, minimizing the risk of future damage. Conclusion Cracks and dents in drywall are avoidable with proper techniques, quality materials, and a focus on preventing structural movement. At Calgary Drywallers , we specialize in durable, flawless drywall installation tailored to Calgary's unique environment. Need expert drywall services? Contact Calgary Drywallers today for a consultation and let us bring your vision to life!
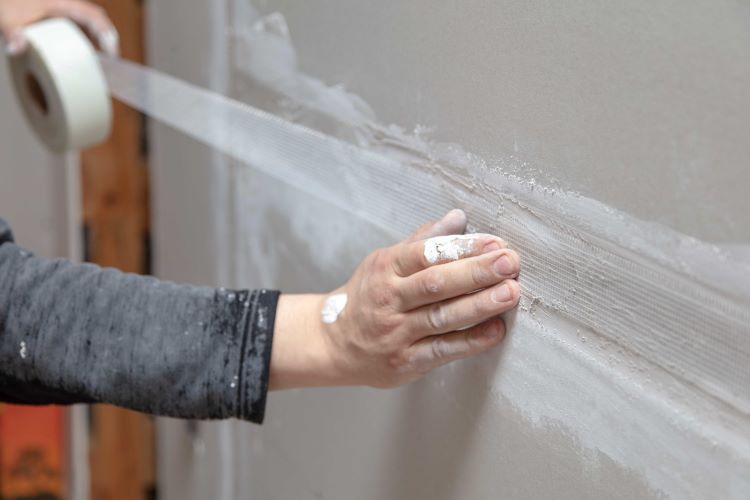
Drywall taping can be a daunting task, especially when dealing with large seams. Large seams require extra attention and precision to ensure a flawless, professional finish. At Calgary Drywallers , we specialize in helping homeowners and contractors achieve perfect results, whether you’re tackling a DIY project or need professional assistance. Here’s a step-by-step guide to taping large drywall seams without errors. Step 1: Gather the Right Tools and Materials Before you begin, ensure you have the following tools and materials on hand: Drywall tape: Choose between paper tape or mesh tape. Paper tape is stronger but requires more skill to apply, while mesh tape is self-adhesive and easier for beginners. Joint compound (mud): Lightweight or all-purpose joint compound works best. Taping knives: A 6-inch knife for initial application and a 10- or 12-inch knife for smoothing. Mud pan: For holding joint compound during application. Sanding block or drywall sander: For a smooth finish after the compound dries. Step 2: Prepare the Seam Preparation is key to successful drywall taping. Clean the seam: Remove dust, debris, and any loose drywall particles from the seam. Check for gaps: For large gaps (wider than 1/4 inch), fill with joint compound first and allow it to dry before taping. Prime the surface: Lightly apply a thin coat of joint compound to create a base for the tape to adhere to. Step 3: Apply the Drywall Tape Cut the tape: Measure and cut a length of tape that fits the seam. Place the tape: For paper tape, embed it into the wet compound you applied during priming. For mesh tape, simply stick it directly to the seam. Smooth the tape: Use your 6-inch taping knife to flatten the tape and remove excess compound, ensuring no bubbles or wrinkles are present. Step 4: Apply the First Coat of Joint Compound Spread the compound: Using your 6-inch knife, apply a thin layer of joint compound over the tape. Feather the edges: Extend the compound slightly beyond the edges of the tape to create a seamless blend with the drywall. Inspect for bubbles: Smooth out any air bubbles or irregularities. Allow this first coat to dry completely, typically 24 hours. Step 5: Apply Additional Coats Switch to a wider knife: Use a 10- or 12-inch taping knife for subsequent coats to feather the compound further out. Build up the seam: Apply two or three thin coats, letting each layer dry before applying the next. Sand between coats: Lightly sand each layer to remove ridges and ensure smoothness. Step 6: Finish and Sand Once the final coat is dry: Sand the seam: Use a sanding block or drywall sander to create a perfectly smooth surface. Inspect your work: Run your hand along the seam to check for any uneven areas or rough spots. Clean up: Wipe away dust with a damp cloth. Pro Tips for Large Drywall Seams Work in manageable sections: Focus on one part of the seam at a time to avoid rushing. Keep your tools clean: Regularly clean your knives and mud pan to prevent dried compound from ruining your work. Use proper lighting: Good lighting will help you spot imperfections as you work. Be patient: Allow each coat to dry completely before sanding or applying the next layer. When to Call the Pros Large drywall seams can be challenging, especially for beginners. If you’re unsure about tackling the task yourself or want a flawless finish, Calgary Drywallers is here to help. Our team of experts has years of experience handling all types of drywall projects, ensuring a professional result every time. Contact Calgary Drywallers today for expert drywall taping services and make your walls look as seamless as possible!
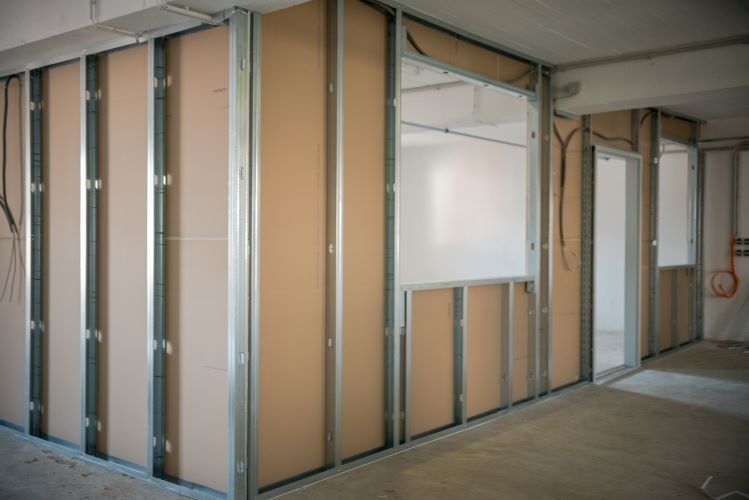
When it comes to building strong and durable walls, the choice of materials for drywall framing is crucial. Traditionally, wood has been the go-to option, but metal studs have been gaining popularity in both residential and commercial construction. At Calgary Drywallers , we’ve seen firsthand the advantages of using metal studs in drywall framing projects across Calgary, Alberta. If you’re considering a renovation or new build, here’s why you should think about metal studs for your next drywall framing job. Why Choose Metal Studs for Drywall Framing? Metal studs are made from galvanized steel, which is lightweight yet incredibly strong. They are designed to support drywall panels and other wall materials while providing a sturdy framework. But what makes them a better option than traditional wood studs? Let’s explore the benefits. 1. Durability and Longevity One of the biggest advantages of metal studs is their durability. Unlike wood, metal studs won’t warp, twist, or shrink over time. They are resistant to moisture, termites, and other pests, making them an ideal choice for Calgary’s varying weather conditions. With metal studs, you can be assured that your walls will remain straight and stable for years to come. Key Benefits: No warping or twisting Resistant to pests and moisture Longer lifespan than wood studs 2. Fire Resistance Safety is always a top priority in construction, especially in residential homes. Metal studs are non-combustible, meaning they won’t catch fire, spread flames, or emit harmful smoke. This fire-resistant quality can be a lifesaver, offering an extra layer of protection to your home or commercial building. Key Benefits: Non-combustible and fire-resistant Enhances the safety of your property Meets building code requirements for fire safety 3. Lightweight and Easy to Handle Another advantage of metal studs is their lightweight nature. They are much lighter than wood, making them easier to transport and handle during the installation process. This not only speeds up the construction timeline but also reduces labor costs. Key Benefits: Easier to carry and install Reduces fatigue for workers Speeds up the framing process 4. Cost-Effective Over Time While metal studs might be slightly more expensive upfront compared to wood, they are more cost-effective in the long run. Their resistance to moisture and pests means fewer repairs and replacements down the line, saving you money on maintenance costs. Additionally, metal studs are often made from recycled materials, making them a more sustainable choice. Key Benefits: Lower long-term maintenance costs Potentially lowers insurance premiums due to fire resistance Eco-friendly and recyclable 5. Consistency and Precision Metal studs are manufactured to precise specifications, ensuring that each stud is straight and uniform. Unlike wood, which can have knots, bends, or other imperfections, metal studs provide a consistent framework for your drywall. This precision makes it easier to achieve a smooth, professional finish on your walls. Key Benefits: Consistent size and shape Eliminates the need for shimming or adjustments Results in a higher-quality finish 6. Better Soundproofing If soundproofing is a concern, metal studs can help. When combined with soundproof drywall and insulation, metal studs can create a more effective sound barrier compared to wood. This makes them an excellent choice for home offices, bedrooms, and commercial spaces where noise control is important. Key Benefits: Enhances soundproofing capabilities Ideal for multi-family residences and office spaces Reduces noise transfer between rooms 7. Resistant to Mold and Mildew Calgary’s fluctuating weather can create moisture issues in homes, leading to mold and mildew growth. Metal studs are naturally resistant to mold, providing a healthier indoor environment. This makes them especially beneficial in basements, bathrooms, and other high-humidity areas. Key Benefits: Reduces the risk of mold and mildew Promotes healthier indoor air quality Ideal for moisture-prone areas 8. Flexibility in Design Metal studs are incredibly versatile and can be used in a wide range of construction projects, from framing walls to creating curved or non-standard designs. They’re easy to cut and shape, allowing for greater flexibility in architectural designs. Key Benefits: Suitable for custom wall designs Easy to cut and modify Supports creative architectural projects Conclusion: Is Metal Framing Right for Your Project? Choosing the right framing material is essential for the success of your drywall project. While wood studs have their place, the benefits of metal studs make them a superior option for many applications, especially in areas prone to moisture, fire, or pest issues. At Calgary Drywallers , we specialize in both metal and wood framing, ensuring that you get the best solution for your needs. If you’re planning a renovation or new build in Calgary, reach out to our team for a consultation. We’ll help you decide if metal studs are the right choice for your project and provide a professional installation that meets the highest industry standards. Contact Us Today! Ready to upgrade your drywall framing? Contact Calgary Drywallers today for a free quote and consultation. Whether you're renovating a basement, building an addition, or starting from scratch, we're here to help you every step of the way.
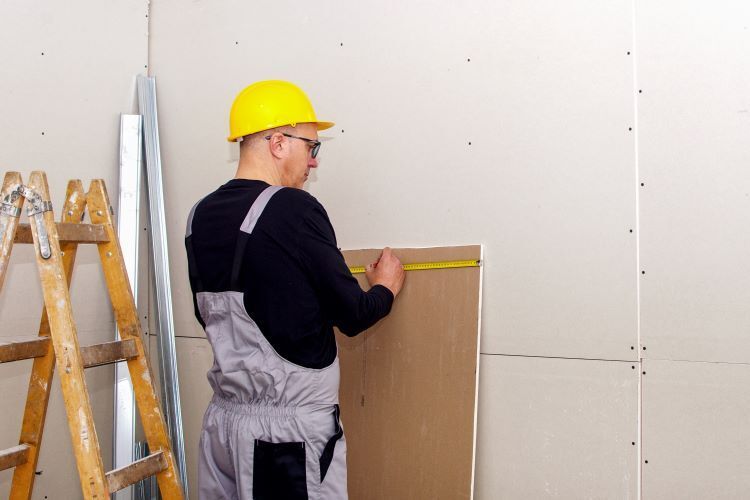
Drywall installation is a vital step in creating smooth, durable walls and ceilings. But what happens when the spaces you're working with are cramped, oddly shaped, or difficult to access? At Calgary Drywallers , we understand the challenges of installing drywall in hard-to-reach areas, whether it’s a narrow hallway, a tricky corner, or a basement crawl space. This guide will walk you through the best practices and techniques to make drywall installation in tight spots as smooth as possible. Why Drywalling in Tight Spaces Is Challenging Hard-to-reach areas present unique challenges that can make drywall installation more complex. These include: Limited Space for Movement: Maneuvering large drywall sheets in tight quarters can be tough. Difficult Angles and Shapes: Areas like stairwells, attics, and alcoves often have awkward angles. Obstructions: Pipes, electrical wiring, and structural beams can obstruct your workspace. Poor Lighting: Limited natural light in these spaces can hinder visibility. But don’t worry—with the right tools, techniques, and a little patience, you can achieve professional-looking results even in the most confined spaces. Tools You’ll Need Before you get started, make sure you have these essential tools: Drywall sheets (usually 4x8 ft or cut to size) Drywall saw or utility knife Drywall T-square for precise cuts Measuring tape Drywall screws and screwdriver Drywall lift (if working overhead) Corner trowel for tight angles Sanding sponge or pole sander Joint compound and taping tools Step-by-Step Guide to Installing Drywall in Hard-to-Reach Spaces 1. Plan Your Cuts and Measurements In cramped spaces, precision is key. Measure the area accurately and plan your drywall cuts to minimize waste. Use a drywall T-square and a utility knife to make clean cuts. If the space is unusually shaped, create a cardboard template before cutting the drywall to fit. Pro Tip: Measure twice and cut once. It’s much easier to trim down a larger piece than to add material later. 2. Cut Drywall to Manageable Sizes Full-sized drywall sheets can be difficult to handle in tight areas, so consider cutting them into smaller, more manageable pieces. While this may increase the number of seams you have to tape, it will make installation much easier. For narrow hallways, cut sheets to fit the width of the space. In areas like crawl spaces, consider using half sheets or smaller sections. 3. Use a Drywall Lift for Overhead Spaces When installing drywall on ceilings in confined areas, a drywall lift can be a game-changer. It allows you to hold the drywall sheet securely in place while you screw it in, saving you time and energy. 4. Start from the Ceiling Down Always begin with the ceiling if you're drywalling an entire room. This provides better support for the wall sheets and helps cover any gaps along the top edges. Secure the ceiling drywall using screws spaced 12 inches apart. Ensure each screw is flush with the drywall surface to avoid bumps. 5. Tackle Tight Corners and Awkward Angles For corners and odd angles, use a corner trowel to achieve smooth finishes. Apply joint compound generously, then use the trowel to create a sharp, clean line. Pre-formed corner beads can also be helpful for achieving professional results. Use flexible drywall tape for unusual angles and curves. Apply joint compound over the tape, smooth it out, and allow it to dry. 6. Secure Drywall Around Obstructions When dealing with pipes, vents, or electrical boxes, you’ll need to cut precise holes in the drywall. Here’s how: Use a drywall saw or a hole saw attachment for circular cuts. Mark the location of the obstructions on the drywall before cutting. Cut slowly to avoid overcutting or damaging the material. Pro Tip: Measure the distance from the edge of the sheet to the center of the obstruction to get accurate placement. 7. Tape and Mud Like a Pro Taping and mudding are crucial for a seamless finish, especially when working with multiple seams in tight spaces. Apply a thin layer of joint compound over the seams and embed the drywall tape into it. Use a 6-inch taping knife to smooth out the compound. Let it dry, sand lightly, and apply two more coats, feathering the edges each time. 8. Sand Carefully in Confined Areas Sanding drywall in small spaces can kick up a lot of dust, so it’s essential to work carefully. Use a sanding sponge for better control in tight corners. Consider a dust-free sanding system or attach a vacuum to your sander if you’re using a power tool. Wear a dust mask and safety goggles for protection. 9. Inspect and Touch Up Once the sanding is complete, inspect the drywall for any imperfections. Fill in small holes or cracks with joint compound, let it dry, and sand again. A quick coat of primer will reveal any remaining flaws that need attention. Final Thoughts: Hire a Pro for Challenging Spaces Drywalling hard-to-reach areas requires patience, precision, and the right tools. While it’s possible to tackle these projects yourself, hiring professionals like Calgary Drywallers can save you time and ensure a flawless finish, especially in challenging spaces. Our experienced team has the expertise to handle even the trickiest drywall installations, ensuring your home looks its best. If you’re in the Calgary area and need help with your next drywall project, give us a call! Why Choose Calgary Drywallers? At Calgary Drywallers , we specialize in providing high-quality drywall solutions for every space in your home. From new installations to repairs, our skilled team is ready to help you achieve the perfect finish. Contact us today for a free consultation! By following these tips and techniques, you’ll be well on your way to successfully installing drywall in those tricky, hard-to-reach spaces. Whether you’re a DIY enthusiast or prefer to leave it to the pros, understanding the challenges and solutions can help you get the best results for your home renovation projects.
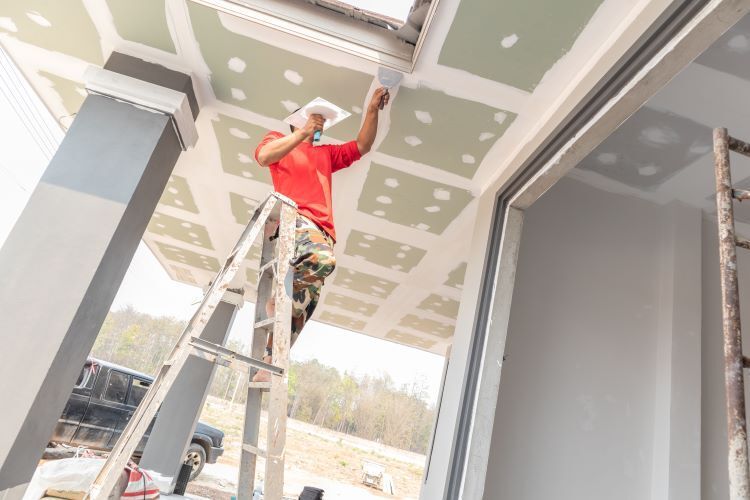
Sagging drywall ceilings can be an eyesore and a sign of underlying issues. Whether it's due to moisture, improper installation, or aging materials, a drooping ceiling not only looks bad but can also pose safety risks. At Calgary Drywallers, we specialize in drywall repair , and today, we’re breaking down how you can address sagging drywall ceilings safely and effectively. 1. Identify the Cause of Sagging Before starting any repair, it’s essential to figure out why your ceiling is sagging. Some common causes include: Moisture Damage: Leaks from above, high humidity, or plumbing issues can weaken the drywall, leading to sagging. Improper Installation: If screws or nails weren't used correctly or weren’t sufficient to hold up the drywall, sagging can occur over time. Aging or Wear and Tear: Drywall materials naturally weaken over time, especially in older homes. Insulation Issues: Heavy or poorly installed insulation can put extra pressure on the ceiling, causing sagging. Understanding the cause helps you decide on the best repair approach and prevents future issues. 2. Gather the Right Tools and Materials Repairing a sagging ceiling requires the right tools to ensure a sturdy, lasting fix. Here’s what you’ll need: Ladder or scaffolding for safe access to the ceiling Drywall screws, ideally 1-¼ inch or longer Cordless drill or screwdriver Utility knife and a drywall saw Joint compound and putty knife Drywall tape Sandpaper (120- to 150-grit) Paint and primer to match the ceiling’s finish 3. Remove Damaged Sections (If Necessary) If the drywall is only slightly sagging, you may be able to reinforce it without cutting out large portions. However, if there’s visible water damage, mold, or if the drywall is too damaged, you’ll need to remove the affected areas. Using a utility knife or drywall saw, carefully cut around the damaged area. Always wear protective gear, as drywall dust can be irritating. If there’s mold, consider contacting a professional, as mold spores can affect indoor air quality. 4. Add Support to the Existing Drywall Use drywall screws to resecure any sagging sections. Insert screws along the existing joists or furring strips every 6–8 inches to pull the drywall up tightly against the ceiling. If the ceiling lacks adequate support, consider installing furring strips or adding additional framing for reinforcement. 5. Patch or Replace the Drywall Section For minor sagging, reinforce the area with additional screws as described. For larger repairs, cut a new drywall piece that fits the hole you removed. Secure it to the joists with screws. Apply drywall tape along the seams between the new drywall piece and the existing ceiling. 6. Apply Joint Compound and Smooth the Surface Use a putty knife to spread a thin layer of joint compound over the taped seams. Feather the edges to blend the new section with the old. After the first layer dries, lightly sand it down, then apply a second coat if needed. Continue sanding until the surface is smooth. 7. Prime and Paint the Ceiling Prime the repaired area to seal it and prevent moisture from penetrating the drywall. This is especially important in areas with high humidity. Once the primer is dry, paint the ceiling to match the surrounding area. Using high-quality ceiling paint helps ensure a seamless finish. 8. Prevent Future Sagging To avoid future issues, consider the following preventative tips: Inspect for Leaks Regularly: Check for leaks in plumbing or roofing, especially after heavy rain or snow. Control Indoor Humidity: Use a dehumidifier if necessary, especially in moisture-prone areas like bathrooms and basements. Ensure Proper Insulation Installation: If your ceiling has insulation, make sure it’s installed correctly to avoid excess weight. When to Call a Professional While minor sagging can often be fixed with basic tools, larger issues may require the help of a professional drywall repair service. If you’re dealing with significant water damage, mold, or structural issues, it’s best to call in the experts. At Calgary Drywallers, we have extensive experience in addressing sagging ceilings and other drywall issues across Calgary. We understand the unique climate challenges here and provide long-lasting solutions to ensure your home looks its best. Conclusion Fixing a sagging drywall ceiling can be a manageable DIY project if you follow the steps carefully and have the right tools. However, when in doubt, remember that professionals can ensure a safe, effective, and aesthetically pleasing repair. If you’re dealing with sagging ceilings or any other drywall concerns, contact Calgary Drywallers for expert guidance and solutions.
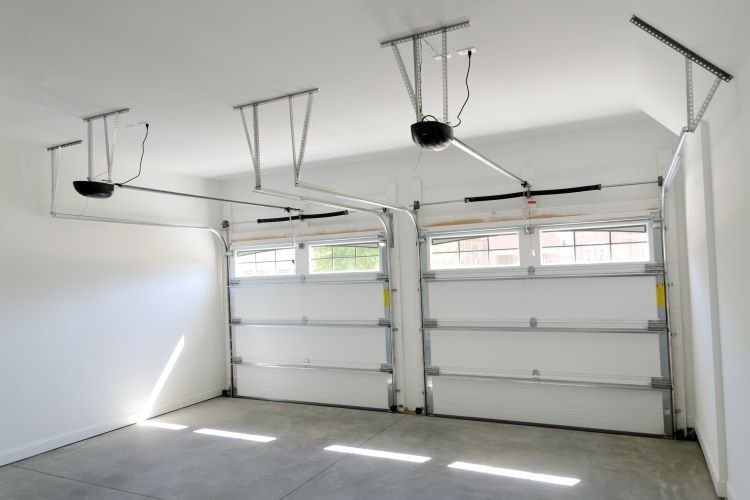
When it comes to finishing a garage, selecting the right drywall is key to ensuring a long-lasting and durable finish. Garages, especially in climates like Calgary’s, often face moisture, temperature fluctuations, and even accidental impacts that can damage standard drywall. Moisture-resistant drywall can provide the extra durability and protection needed to keep your garage walls in great condition. Here, we’ll explore some of the best moisture-resistant drywall options available, their benefits, and tips for achieving an efficient, long-lasting installation. Why Moisture-Resistant Drywall for Garages? Garages are especially vulnerable to dampness, whether from water runoff, snow, vehicle condensation, or humidity changes. Regular drywall can swell, crack, or develop mold in these conditions, leading to costly repairs. Moisture-resistant drywall types, such as green board, purple board, and cement board, provide enhanced protection against these elements and ensure that your garage walls maintain their appearance and functionality over time. Top Moisture-Resistant Drywall Options for Garages Green Board Drywall Best for: General moisture resistance. Description: Known for its green color, green board is a type of drywall treated with a water-resistant coating, making it less likely to absorb moisture. While it’s not waterproof, green board works well in spaces with occasional humidity, such as garages, bathrooms, and basements. Pros: Cost-effective, widely available, suitable for mildly humid areas. Cons: Not suitable for areas with constant water exposure. Purple Board Drywall Best for: High mold and mildew resistance. Description: Purple board takes moisture resistance a step further by incorporating mold inhibitors, making it a top choice for areas with potential mold issues. This drywall also resists impact, which is an added benefit in a garage setting. Pros: High resistance to mold and mildew, durable and impact-resistant. Cons: More expensive than standard drywall or green board. Cement Board Best for: Maximum moisture and water resistance. Description: Cement board is made of a cement-based composite with fiberglass reinforcement. It’s entirely waterproof, making it ideal for areas where water exposure is likely. It’s a popular choice in showers and wet rooms, and it can be effective in garages, particularly for lower wall areas that might get wet. Pros: Extremely durable, waterproof, resistant to mold and mildew. Cons: Heavier and more challenging to install, higher cost. Fiberglass-Faced Drywall Best for: Mold resistance and durability in humid environments. Description: Unlike traditional paper-faced drywall, fiberglass-faced drywall eliminates the organic material (paper) that can attract mold and mildew. This material performs well in spaces with frequent temperature changes, like garages, and is a great alternative for walls that might see occasional moisture. Pros: Highly mold-resistant, durable, suitable for variable temperatures. Cons: Higher cost, installation can be more challenging without professional help. Benefits of Moisture-Resistant Drywall in Garages Using moisture-resistant drywall in your garage offers several important benefits: Improved Mold Resistance: With the right drywall, you can reduce the risk of mold and mildew growth, keeping your garage healthier and safer. Greater Durability: Moisture-resistant drywall options are often designed to withstand impacts, which is ideal for high-traffic areas where tools and equipment may bump or scrape against walls. Lower Maintenance: Since moisture-resistant drywall is less likely to warp or require frequent repairs, you’ll save on upkeep in the long run. Installation Tips for Moisture-Resistant Drywall Seal the Joints Properly: Use a high-quality joint compound and fiberglass or waterproof tape to seal seams, corners, and edges. This will help prevent water from seeping into the seams and causing swelling or mold. Add a Vapor Barrier: If your garage has high humidity levels, consider installing a vapor barrier behind the drywall. This extra layer can help block moisture from reaching the drywall, offering additional protection. Ventilate: Ensuring proper ventilation in your garage is key to preventing moisture buildup. Install vents or use a dehumidifier to keep humidity levels low, further safeguarding your moisture-resistant drywall. Consider Mold-Resistant Paint: Once the drywall is up, apply a mold-resistant primer and paint. This will give you an added layer of defense against moisture and mold. Selecting the Best Option for Your Garage’s Needs Choosing the right moisture-resistant drywall for your garage depends on factors like your budget, the level of moisture exposure, and the typical climate. Here’s a quick guide: For Moderate Moisture Protection: Green board is an affordable choice for general moisture resistance. For High Humidity and Impact Protection: Purple board offers robust mold and mildew resistance and is durable enough for garage environments. For Extreme Moisture Protection: Cement board provides the best waterproofing but requires a more involved installation process. For Variable Climate and Humidity: Fiberglass-faced drywall is an ideal option if your garage experiences wide temperature swings or condensation. Professional Installation for Best Results For most homeowners, installing drywall—especially moisture-resistant types—can be a complex and labor-intensive job. Professional drywallers, like Calgary Drywallers, are skilled in selecting the right materials, ensuring proper installation, and addressing the unique challenges of garage environments. Professionals can also help you choose the best drywall type based on your budget and specific needs. Conclusion Using moisture-resistant drywall in your garage is a practical way to prevent costly issues from water damage, mold, and mildew. Whether you opt for green board, purple board, cement board, or fiberglass-faced drywall, each type offers unique benefits to suit different needs and conditions. Proper installation and maintenance will help keep your garage walls in top shape, providing a durable and long-lasting finish that stands up to the elements. For help with selecting the right moisture-resistant drywall and expert installation in Calgary, reach out to Calgary Drywallers . With the right materials and expertise, we’ll ensure your garage walls are built to withstand Calgary’s diverse climate conditions.
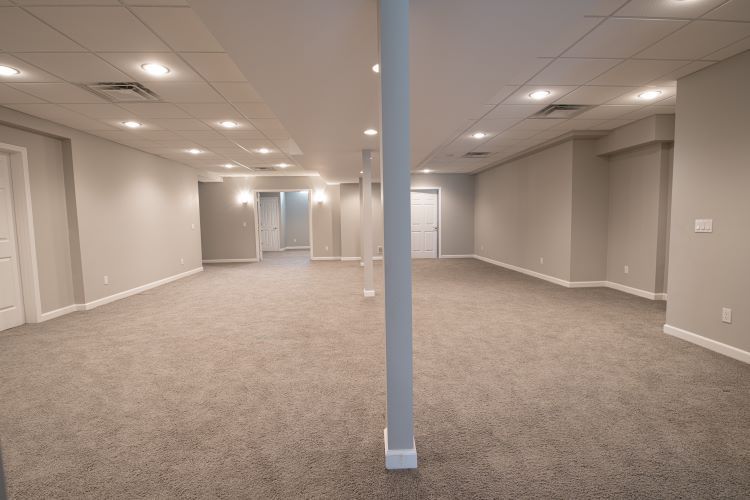
When it comes to finishing your basement, the drywall texture you choose can make a significant impact on the overall feel and aesthetic of the space. Whether you're transforming your basement into a cozy living area, a home office, or a recreational room, selecting the right drywall texture can add character and complement your design vision. At Calgary Drywallers , we understand how important it is to create a polished, inviting space in your home, especially when it comes to a basement remodel. In this article, we’ll guide you through the different types of drywall textures and how to choose the one that best suits your needs. Why Drywall Texture Matters Drywall texture is more than just a finishing touch. It can help disguise imperfections, enhance lighting, and add depth to your basement walls . Because basements often serve as multipurpose areas, it's crucial to pick a texture that not only matches the design style of the room but also serves a functional purpose. The right texture can contribute to the room’s overall durability and help reduce maintenance needs in the long run. Popular Drywall Textures for Basements Here are a few common drywall textures to consider for your basement renovation: 1. Smooth Finish A smooth finish is sleek, modern, and timeless. This texture offers a flat, even surface that provides a clean look and works well in contemporary or minimalist designs. However, a smooth finish can show imperfections more easily than other textures, making it important to ensure proper installation and finishing. If you're aiming for a polished and elegant appearance, the smooth finish may be perfect for your basement walls. Best for: Modern designs, minimalistic spaces, and areas where lighting is key. Pros: Clean, sophisticated appearance. Cons: Imperfections may be more noticeable; requires skilled application. 2. Knockdown Texture Knockdown texture is a popular option for basements due to its unique look and ability to hide imperfections. It features a slightly raised, uneven pattern that adds subtle dimension to the walls. Knockdown is applied by spraying or rolling the drywall compound onto the wall, then "knocking down" the raised portions to create a textured, yet refined finish. Best for: Family rooms, entertainment areas, or any space where durability is important. Pros: Hides imperfections; easy to maintain. Cons: Requires a bit more labor than a smooth finish. 3. Orange Peel Texture Orange peel texture resembles the skin of an orange, with a slightly bumpy, stippled appearance. This texture is applied with a sprayer, creating a uniform pattern that provides visual interest without being overwhelming. It’s a common choice in basements because it helps conceal minor flaws while maintaining a relatively smooth surface. Best for: Multipurpose rooms, children’s play areas, or basements with low ceilings. Pros: Hides minor imperfections; easy to clean. Cons: May not suit all design styles. 4. Popcorn Texture While popcorn ceilings are often considered outdated, some homeowners still opt for this texture on walls in certain areas, including basements. Popcorn texture has a rough, bumpy surface that’s excellent at soundproofing, which makes it a practical choice if you're converting your basement into a home theater or music studio. However, it can be harder to clean and maintain. Best for: Basements used for media rooms or soundproofed spaces. Pros: Excellent sound absorption. Cons: Difficult to clean; outdated in some design trends. 5. Skip Trowel Skip trowel is a highly artistic and decorative texture that creates a sophisticated look with irregular, sweeping patterns across the walls. This technique requires a skilled professional to apply and is ideal for homeowners who want to add a touch of elegance to their basement without opting for a fully smooth finish. The texture is applied by using a trowel to “skip” across the surface of the drywall, leaving behind a thin layer of compound. Best for: Stylish and elegant basements, such as home offices or entertainment spaces. Pros: Elegant appearance; hides wall flaws. Cons: More labor-intensive to apply. Factors to Consider When Choosing a Texture When choosing a drywall texture for your basement walls, it's important to consider several factors: Functionality: Consider how the room will be used. If your basement serves as a home theater or music room, textures like popcorn or knockdown, which offer soundproofing benefits, might be ideal. For a cleaner, modern look in a home office or living space, a smooth or orange peel texture may be more suitable. Maintenance: Some textures are easier to clean and maintain than others. For high-traffic areas or basements that may experience more wear and tear, knockdown or orange peel textures can be more forgiving. Smooth finishes, on the other hand, require more maintenance to keep looking pristine. Aesthetic Appeal: Your design style will heavily influence which texture works best. If you prefer a modern, sleek look, a smooth finish is ideal. For a more traditional or rustic aesthetic, consider textured finishes like skip trowel or knockdown. Budget: Certain textures, like skip trowel or knockdown, require more labor and expertise to apply, which may affect the cost. Simpler textures like orange peel or smooth finishes may be more budget-friendly options for your basement drywall project. Conclusion Choosing the right drywall texture for your basement walls can dramatically influence the final look and feel of the space. Whether you're looking for something sleek and modern or textured and durable, there are plenty of options to suit your design and functional needs. At Calgary Drywallers , we specialize in helping homeowners choose and apply the perfect drywall textures for their basement renovations. Contact us today to learn more about how we can help transform your basement into a beautifully finished space.
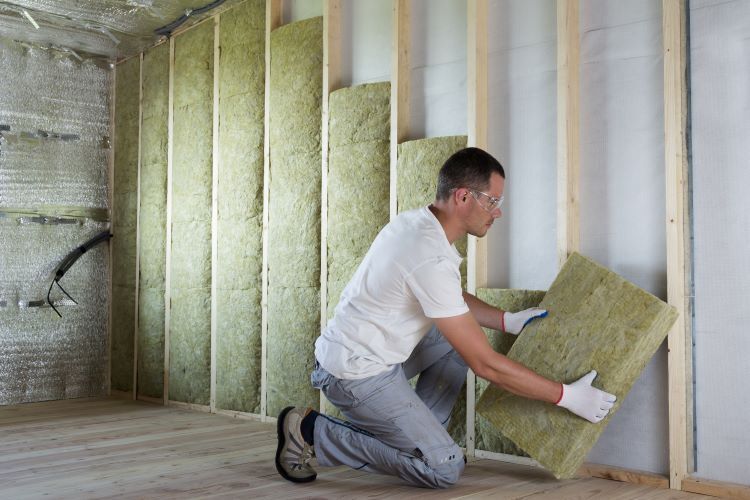
If you’re a homeowner in Calgary, you know how important it is to maintain a comfortable, energy-efficient home, especially with the extreme fluctuations in temperature throughout the year. One of the most impactful but often overlooked aspects of home comfort is the quality of your drywall insulation. Over time, insulation can degrade or become less effective, leading to higher energy bills, drafty rooms, and uneven indoor temperatures. But when should you consider upgrading your drywall insulation? Let’s explore the key signs that it’s time for an upgrade, the benefits of making the change, and how professional help can ensure the job is done right. Signs It's Time to Upgrade Your Drywall Insulation Inconsistent Indoor Temperatures If certain rooms in your home are colder or hotter than others, your insulation may not be performing at its best. Poor or outdated drywall insulation often allows heat to escape or enter through the walls, causing temperature imbalances throughout your home. High Energy Bills If your heating or cooling bills are steadily increasing, poor insulation could be the culprit. Worn-out or insufficient insulation forces your HVAC system to work harder to maintain a stable indoor temperature, which leads to higher energy consumption. Drafty Walls Have you noticed cold drafts coming from your walls, even though your windows and doors are sealed? This is often a sign that the insulation inside your drywall is no longer effective at keeping the cold air out. Moisture and Mold Problems Proper insulation also helps regulate humidity levels inside your home. If you’re seeing signs of mold, dampness, or condensation on your walls, it may indicate that your insulation isn’t doing its job. Mold growth, in particular, can lead to more significant issues, including health risks and structural damage. Older Home If your home was built more than 15–20 years ago and hasn’t undergone any insulation upgrades, it’s likely that the insulation materials have aged and are no longer up to modern energy efficiency standards. Newer insulation technologies provide superior performance, so an upgrade could be a great investment. Benefits of Upgrading Drywall Insulation Improved Energy Efficiency Upgrading your drywall insulation can make a huge difference in reducing energy loss. Modern insulation materials are designed to better trap heat in the winter and keep your home cool in the summer, reducing the load on your HVAC system. Lower Energy Bills With better energy efficiency comes lower energy costs. By upgrading your insulation, you can significantly cut down on your monthly utility bills, offering a quick return on investment. Enhanced Comfort Proper insulation ensures that your home maintains a consistent and comfortable temperature throughout all seasons. No more dealing with hot or cold spots around your home. Increased Home Value Insulation upgrades are an excellent selling point if you’re considering putting your home on the market. Prospective buyers appreciate energy-efficient features, and knowing that they won’t have to worry about future insulation problems adds value. Improved Soundproofing One often-overlooked benefit of upgrading insulation is sound reduction. Modern insulation materials can help dampen noise between rooms and from the outside, making your home a quieter, more peaceful environment. When to Call a Professional Upgrading your drywall insulation is a job that requires careful planning and expertise. While some homeowners may attempt DIY projects, insulation installation and upgrades are best left to professionals, especially in a climate like Calgary’s, where insulation plays a crucial role in year-round comfort. Here are a few reasons to call in professional drywall contractors: Expert Assessment: Professionals can assess your current insulation to identify gaps, inefficiencies, or outdated materials that need replacing. Proper Installation: Installing insulation isn’t just about placing material between walls. It requires precision to ensure there are no gaps, uneven areas, or mistakes that can compromise efficiency. Code Compliance: Professional contractors are familiar with local building codes and ensure that your insulation meets or exceeds the necessary standards. Material Knowledge: There are different types of insulation materials available, such as fiberglass, spray foam, and blown-in insulation. A professional can recommend the best option for your home’s specific needs and climate conditions. Conclusion If you’re noticing cold drafts, higher energy bills, or mold problems in your Calgary home, it might be time to upgrade your drywall insulation. The benefits go beyond energy savings — you’ll enjoy a more comfortable, quieter, and valuable home. By partnering with experienced professionals like Calgary Drywallers, you can ensure that your insulation upgrade is done right the first time, bringing lasting comfort and efficiency to your living space. Take the first step towards a more energy-efficient and comfortable home by contacting Calgary Drywallers today!
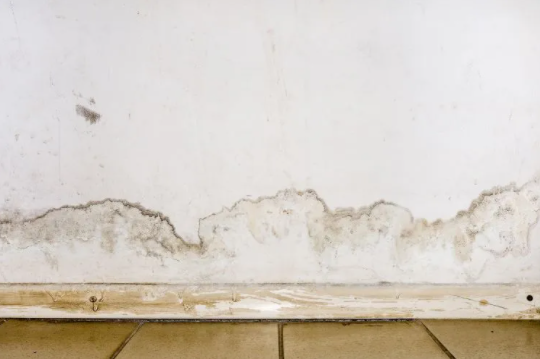
Water damage is one of the most significant threats to the structural integrity of your home, especially when it comes to drywall and ceilings. These essential components of your home’s construction are highly susceptible to moisture, and when compromised, they can lead to costly repairs, health risks, and long-term issues. In this article, we’ll explore how water damage affects drywall and ceilings and provide tips on how to identify, prevent, and address these problems. Why Drywall and Ceilings are Vulnerable to Water Damage Drywall is a commonly used material for interior walls and ceilings because of its affordability, ease of installation, and smooth finish. However, it is not water-resistant. Drywall is made of gypsum, which absorbs moisture quickly. This can cause the material to weaken, swell, or even crumble if exposed to prolonged moisture. Ceilings, especially those made from drywall, are just as vulnerable as the walls. When water damage occurs, the weight of the absorbed water can cause the ceiling to sag or collapse, posing a serious safety risk to homeowners. Common Causes of Water Damage in Drywall and Ceilings Water damage can result from several factors, including: Plumbing Leaks: Hidden leaks behind walls or in ceilings from broken pipes, faulty plumbing, or dripping faucets are common causes of water damage in drywall. Roof Leaks: A leaky roof can allow water to seep into your ceiling and walls, causing extensive damage, especially during heavy rainfall or after snow melts. Burst Pipes: A sudden pipe burst can release large amounts of water, quickly saturating drywall and ceilings. Flooding: Whether due to natural disasters or household accidents, flooding can wreak havoc on drywall and ceilings if not addressed immediately. Condensation: Poor ventilation in areas like bathrooms, kitchens, or basements can lead to condensation buildup, which can damage ceilings and walls over time. The Dangers of Ignoring Water Damage When left unchecked, water damage can cause serious issues with your drywall and ceiling integrity. Here are some of the dangers: Structural Weakness: When drywall absorbs too much water, it loses its strength, becomes soft, and may start to crumble. This compromises the structural integrity of the affected area, leading to sagging ceilings, collapsing walls, and a potential safety hazard. Mold Growth: Moisture trapped in drywall creates the perfect environment for mold and mildew growth. This not only damages your home but also poses significant health risks, including respiratory problems and allergic reactions. Aesthetic Damage: Water damage often results in unsightly stains, discoloration, and warping on walls and ceilings. It can ruin the overall appearance of a room, requiring significant restoration work to restore the space’s aesthetic appeal. Expensive Repairs: What may start as a minor leak can quickly turn into a costly repair job if left unattended. Sagging ceilings and deteriorating drywall will require extensive labor and materials to fix, driving up repair costs. Signs of Water Damage in Drywall and Ceilings Early detection is key to minimizing damage and repair costs. Here are some signs that you may have water damage in your drywall or ceiling: Discoloration: Yellow or brown stains on your ceiling or walls are a clear indication of water damage. These stains are often found in areas directly below plumbing lines or roofing. Sagging: A ceiling or wall that appears to be sagging or bulging is likely saturated with water and may be at risk of collapse. Peeling Paint or Wallpaper: If paint or wallpaper starts to bubble, peel, or crack, this can indicate moisture behind the drywall. Musty Odor: A persistent musty smell in a room, even if you can’t see the water damage, is often a sign of mold or mildew growing behind the walls or ceiling. How to Address Water Damage in Drywall and Ceilings Once you’ve identified water damage, it’s important to take action quickly to prevent further damage: Stop the Source of the Water: First and foremost, identify and stop the source of the water intrusion. This could mean repairing a leaking pipe, fixing the roof, or improving ventilation in moisture-prone areas. Assess the Damage: Depending on the extent of the damage, you may need to remove and replace the affected drywall or ceiling material. If the damage is minor, professional drying techniques may be sufficient to salvage the area. Dry Out the Area: Use fans, dehumidifiers, and proper ventilation to dry out the damaged area thoroughly before making repairs. Failing to dry the area properly can lead to mold growth. Repair or Replace the Drywall/Ceiling: For minor damage, drywall patches or ceiling repairs may be enough. However, for extensive damage, you’ll likely need to replace entire sections of drywall or ceiling to ensure structural integrity. Consider Waterproof Drywall: In areas that are prone to moisture, such as basements, bathrooms, and kitchens, consider using moisture-resistant drywall (also known as green board or purple board) to provide added protection against future water damage. Preventing Future Water Damage Once you’ve repaired the damage, it’s crucial to take steps to prevent it from happening again. Here are some tips to safeguard your drywall and ceilings from water damage: Regular Roof Inspections: Make sure your roof is in good condition and check for any signs of damage or leaks, especially after storms. Maintain Plumbing: Regularly inspect your home’s plumbing for any leaks or signs of wear and tear. Address any issues promptly. Install Proper Ventilation: Ensure that areas prone to humidity, such as bathrooms and kitchens, are well-ventilated to prevent condensation buildup. Monitor Humidity Levels: Use a dehumidifier in areas like basements to keep moisture levels in check. Conclusion Water damage can severely affect the integrity of your drywall and ceilings, leading to structural problems, mold growth, and costly repairs. By understanding the risks and taking prompt action, you can protect your home and avoid further damage. If you suspect water damage in your home, don’t wait—contact Calgary Drywallers for expert assessment and repair services. We’ll help you restore your home’s structural integrity and keep it safe from future water damage.
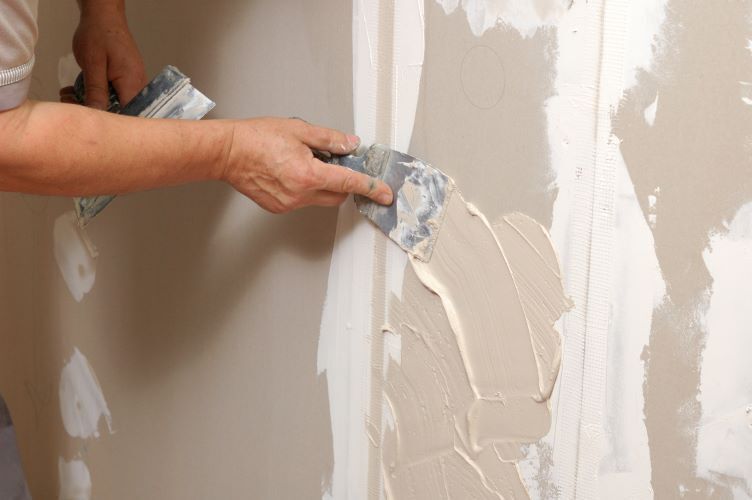
When it comes to achieving that flawless drywall finish, one of the most important steps is applying the right number of coats of drywall mud , also known as joint compound. At Calgary Drywallers, we understand that a smooth, seamless wall is key to a professional finish, and knowing how to properly apply drywall mud plays a big part in that. But how many coats of mud do you actually need for perfect drywall? The answer depends on the condition of the drywall, the type of mud being used, and your desired finish. Below, we’ll walk you through the typical number of coats and offer tips for each stage of the process. The Basics of Drywall Mudding Drywall mud is applied to cover the seams between drywall sheets, as well as to conceal screws, nails, and other imperfections. The goal is to create a perfectly smooth, even surface that’s ready for priming and painting. Here’s the general process for mudding drywall: Taping the Seams: The first step is embedding drywall tape into the seams between the drywall sheets using a layer of mud. This helps reinforce the joints and prevents future cracking. Applying Multiple Coats: Once the tape is set, multiple coats of mud are applied, each one being sanded and smoothed before the next. Each layer serves to gradually build up a smooth surface. Final Sanding: After the last coat has dried, the surface is sanded to perfection before priming and painting. How Many Coats Are Needed? Typically, drywall finishing requires three coats of mud to achieve a smooth, professional finish. However, some situations may call for additional coats. Here’s a breakdown of the typical stages: 1. First Coat (Tape Coat) The first coat is applied after taping the seams. A thin layer of joint compound is spread over the tape to embed it into the drywall. This coat fills in the gaps and covers fasteners like screws and nails. It’s important to keep this coat as thin as possible since it’s mainly for embedding the tape, not for smoothing out the surface. Tips: Use all-purpose or quick-setting mud. Smooth the mud evenly, and wipe away excess for a thin, clean coat. Allow it to dry fully before moving on. 2. Second Coat (Filling Coat) The second coat is your first real chance to smooth out the surface. This coat is applied over the seams and fasteners, gradually widening the coverage area to blend it with the surrounding drywall. You’ll want to feather the edges so the transition between the mud and drywall is invisible. Tips: Use a wider drywall knife (8-10 inches) for this coat. Apply the mud smoothly and avoid ridges or lines. Let this coat dry thoroughly before sanding lightly to knock down any high spots. 3. Third Coat (Finishing Coat) The final coat should be the smoothest and thinnest. This coat is designed to perfect the surface, filling in any remaining imperfections and ensuring a seamless transition between the mudded areas and the drywall. This coat is key to achieving a flawless finish. Tips: Use a 12-inch or wider knife for this coat to cover a larger area with fewer strokes. Keep the mud thin and smooth, focusing on blending everything together for an even surface. 4. Sanding and Final Touches Once the final coat is dry, the surface should be lightly sanded to eliminate any remaining imperfections. After sanding, wipe the walls down with a damp cloth to remove dust and prepare the surface for priming. Tips: Use fine-grit sandpaper (180-220) and avoid over-sanding, which can expose the drywall tape. When Are Additional Coats Needed? While three coats are generally sufficient for most drywall projects, some situations may require additional coats. Here’s when you might need more than three coats: Dealing with uneven surfaces: If the drywall was installed unevenly, additional coats may be needed to level out the surface. Fixing mistakes: If previous coats were not applied smoothly or dried with ridges, additional coats can help fix imperfections. Textured finishes: If you’re going for a textured finish, you may need more coats to build up the desired texture and achieve consistency. Professional Drywall Finishing in Calgary At Calgary Drywallers, we pride ourselves on delivering smooth, flawless drywall finishes for homes and businesses across the Calgary area. Applying the right number of coats of drywall mud is crucial to achieving that perfect, seamless look. Whether you’re finishing new construction or repairing existing drywall, our team of experts ensures every project meets the highest standards of quality. Conclusion Achieving perfect drywall isn’t just about how many coats of mud you apply, but also about using the right techniques and materials for each coat. While three coats are standard, the condition of the drywall and your desired finish may affect the process. For a professional finish, it’s always a good idea to consult with drywall experts who understand the ins and outs of drywall mudding. Need help with your drywall finishing project in Calgary? Contact Calgary Drywallers today to get a seamless, high-quality result that will leave your walls looking perfect!